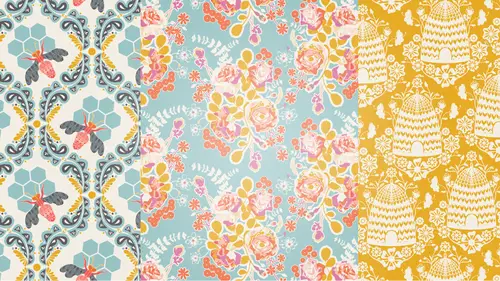
Lessons
Day 1
1The World of Surface Pattern Design
35:40 2Living Your Creative Dream
22:15 3Introduction to Illustrator
27:16 4Basic Tools: Pen, Text, & Blob
22:28 5Color & Function Tools
32:27 6More Tools: Rotate, Duplicate, & Replicate
19:16 7Custom Color Palettes
18:49Essential Tools for Pattern Making
41:59 9Tools for Sketching Inspiration
27:50 10Inspire & Nourish Your Creativity
34:55Day 2
11Creating Objects from Scanned Sketches
17:04 12Tracing & Coloring Sketches
30:46 13Tracing & Coloring with the Pen Tool
37:44 14Working from a Photograph w/ Live Trace
36:24 15Hand Tracing Over Photographs
31:27 16Building Pattern Tiles in Illustrator
21:13 17Adding Textures to Illustrations
28:52 18An Unrefined Look in Illustrator
26:10 19Typography & Students Homework
21:39 20Legality of Design w/ Annie Tunheim
27:33 21Trademark & Licensing w/ Annie Tunheim
27:50Day 3
22How to Design Repeating Patterns
18:52 23Complex Cluster Patterns - Part 1
27:38 24Complex Cluster Patterns - Part 2
28:35 25Getting Noticed: Portfolios & Trade Shows
39:43 26How to Drape on Pattern Mock Ups
19:07 27Fun Stuff: Desktop Backgrounds
19:42 28Fun Stuff: Gift Cards & Tags
29:05 29Fun Stuff: Clip Art & Shipping Labels
28:17 30Spoonflower: Stephen Fraser
29:04 31Uploading Patterns for Web Printing
20:29Lesson Info
Spoonflower: Stephen Fraser
We are introducing Stephen from Spoonflower and he is going to join us to talk about all that you guys do, hey Stephen. Hi Bonnie how's it going? Great how are you? I'm doing well, it's nice to be here. Good we are so excited to have you here and I don't know how many people in the audience have used Spoonflower, but I have used you guys for years, you catapulted my career in surface pattern design when I had nobody else to turn to, you guys were there. I could get yardage of fabric and I still, just ordered some the other day, I still use you guys. And absolutely love the work that you do. So I'm excited to introduce audience if everybody doesn't know you, but I have a feeling that most people do. Well I like to think that Spoonflower is the second best quilt shop in the world. Yes. (laughing) Yeah I'll give you that, I'll give you that. So why don't you just introduce yourself I would love to hear your story and how you got involved with Spoonflower and how it all came ab...
out. Sure well, Spoonflower we started it, my business partner and I started it six years ago in 2008. And in fact at the time neither of us knew a thing about fabric, or a thing about sewing, or a thing about printing, and it's probably also worth noting that we didn't have much money to start with, so the odds were stacked well against us in terms of success, as start-ups go. But I have a wife who is a fabric person and who loves sewing, and loves making things with fabric, and really the idea for Spoonflower came from her, she wanted to make a new set of curtains for our den and she had envisioned in her mind fabric with giant yellow polka dots and she could not find and fabric with polka dots as big as she was imagining, and she said to me one night after work you know I could design this, I could draw this if there was a place where I could just get it printed. That struck me as odd because with the internet, even in 2008, you could get pretty much anything printed. Coffee mugs, mouse pads, calendars, whatever you wanted, so it seemed odd to me that you couldn't get fabric printed. I knew a little bit about this business model because I had worked for another startup, called Lulu.com I don't know if you've heard of that, but Lulu is somewhat similar to Spoonflower in that people can upload things to the internet, make them available for sale to other people, and get them printed on demand and if the difference is Lulu is really all about books. Including comic books. So you know I had this background in internet business models and I thought well somebody could do that with fabric, it can't be that hard to print fabric, right? And I was lucky in that I didn't know what I didn't know, so I persuaded my business partner Garth Davis to join me in the endeavor, and we started out in an old sock mill in Mebin, North Carolina. One room, very atmospheric, brick walls, arched windows, dusty wooden floors, and great textile history. We actually rented it not for the history, but because we could get it month per month and it cost about 75 cents per square foot. And we bought one printer and we figured we would figure out how to use it as we went along. There were many trials and tribulations, dusty old sock mills typically don't have heat or air conditioning to speak of, and dust is very bad for printers, so we ended up buying a tent from Walmart and putting the tent up inside the room and putting the printer inside the tent. And we learned as we went along. The New York Times featured Spoonflower on the cover of it's home section in January, 2009. And at the time we had two part time employees, two printers that didn't work very well, and very little probability of succeeding, especially since we couldn't get loans to buy more printers. We survived by the skin of our teeth and the one thing we always had going for us was, this community around the world that not only loved fabric, but who loved surface design and are passionate about it. I remember a woman telling me when we started, 70 something year old woman, well that's just the greatest idea, all my life I dreamed about designing fabric, in fact that's what I do at night in my mind to help myself fall asleep. And she was just so happy to for the first time, actually have the opportunity to actually be able to design fabric, and Spoonflower provided that opportunity for the first time to artist and creative people, creative tinkerers, as I like to think of them, all over the world. And so with all the struggles that we had in terms of getting, whether learning how to print fabric and learning how to build a manufacturing operation from scratch with no money, we never doubted that we were on to a powerful idea that lots and lots of people would be interested in. And today Spoonflower has over 1,000,000 members and hundreds of thousands of fabric designs available for sale in its marketplace. And we have over 100 employees here in Durham, North Carlina where we have an office that has air conditioning actually. (laughing) I'm actually sitting in the green house, which is a room that we use for community events. Here we have sewing classes and the quilt builds, local quilt builds meet here. We have kids sewing classes so we invite people to come in and use this room, as a sort of way of giving back to the DIY community. Yeah and we're having a lot of fun, should not feel bad. Stephen I love your story and I love the room that you're sitting in. Thank you. So do you have yellow polka dotted curtains in your dinning room now? You know what's funny about that is, Kim did design some fabric in fact she learned Photoshop when we started Spoonflower just so she could design fabric, but once we launched the marketplace where designers could make their own work available to other people, suddenly she found that she was able to find designs that she liked better than the ones she was imagining herself, in the marketplace, so we have lots of Spoonflower fabric on our curtains. And elsewhere on our house, but not yellow polka dots. And you mentioned this but I just want to highlight the fact that you guys are in Durham, North Carolina and so everything is printed right here in the U.S. That's right. Yeah. So I want to get in, just in case people are hearing about you for the first time, which I kind of doubt is the case, but in case they are, tell us a little about what services Spoonflower offers exactly. I know you do fabric and wallpaper and things like that. Yeah that's right so you can use Spoonflower to create your own designs, upload your own designs and have them printed on fabric, wallpaper, or gift wrap. We have at this point, 15 different fabrics to choose from. So there's a variety of cottons, including some organic cottons, some heavier cottons like twill, there's a linen cotton blend, there's a cotton silk blend, there's a silk machine, but they sort of the flagship fabric for us is Kona cotton which is produced by Robert Kaufman. Lots of cottons and then we've recently been introducing some synthetic fiber fabrics that we are sourcing very carefully, so these are as we like to say, not your grandmother's polyester. Probably your grandfather's polyesters. But there actually... Fabrics and one of them, two of them actually that we just launched, faux suede and eco canvas are also great for upholstery. So these are yeah the fabric line is expanding all the time. The wallpaper we have two different wallpaper options, the peel and stick and the water activated, both of which are printed PVC free, materials using very eco friendly inks like everything else we do. And the gift-wrap, which is quite nice for scrapbookers as well as people wrapping presents, it's nice heavy paper, something that we rolled out last year as well. Nice, I have had the opportunity to feel of the two new ones that you just released, the faux suede and the eco canvas, is that what you call that? That's right. They're both, I can attest personally, they are so nice, but my favorite is the organic cotton that's my go to that I get printed with you guys and it has a really luxurious feel to it. So take us through the steps a little bit, first what opportunity you guys give us, I know that you print in small, as small increments as one yard I believe for fabric. Actually you can order just a swatch from us, an eight by eight square is the smallest amount you can order from us, and that costs $5.00. Perfect, and then you also offer us the possibility of opening up a Spoonflower shop. That's right, so you can choose, the default is that your designs are private and they're your own, but you can choose to make your designs visible to the public, and you can choose on top of that to make them on sale to other people. If you sell fabric through the Spoonflower marketplace, you earn a 10% commission on each sale, so at this point we have hundreds of thousands of fabrics in the marketplace and of course we have hundreds of thousands of designs, and you can get any of those printed on any of our fabrics. So it's become a very, very very large quilt shop. Yes. (laughing) It probably, we have the world's leading supply of zombie themed fabrics. There are things you can find on Spoonflower that you will not find anywhere else. Yeah, yeah it really does present us with such a unique opportunity to be able to not only get our own patterns printed, but printed quickly, even if it's for something that you just can't find anywhere else, like you want a particular knit for one project, this is your go to place for that. Tell us a little bit about, I believe the reason that you're able to print such small increments is because you are, correct me if I'm wrong, digitally printing, which is a little bit different than the traditional way of printing fabric? Yeah digital printing, so if you can imagine the printers that we have here in our office are like big versions of the Ink Jet printer that you probably have on your office desk. And just as you can print a photo on your Ink Jet printer in your office, you can print a photo on fabric using our Ink Jet printers. So they're just very large versions of that, that little printer that you're familiar with. The way digital technology works, you take an image or a file that's a piece of digital content and you can print, print it directly on the the media with no minimum, so you can print one of everything. You know one yard of one design, and you can do that 10,000 times and do a different design each time never repeating, so in that sense it's sort of the opposite of mass manufacturing, the mass manufacturing sort of norm for fabric, is really screen printing. Where for every color or element in the design, they engrave a screen, which is a big cylinder, and they fill it with one color and the fabric runs through all the screens very very quickly and once you've engraved those screens and you test it and you've created your tubs full of color, it's very inexpensive to create more of that fabric, so really at that point the cost of the fabric is just raw fabric flying through the process. But to make that cost efficient, you have to do a couple of thousand yards, it's very hard to do less than that. So in that way, mass manufacturing and digital printing sort of have opposite strengths. In digital there's no minimum, but it's very expensive, there's no economy of scale so when you get to that 10,000th yard of fabric it's no less expensive than the first yard of fabric. But with rotary screen printing, which is how most of the fabric in the world gets produced, you can't do one yard, you can't do less than 2,000 yards, but the more yards you run through it, the less expensive each yard becomes. Yeah that helps tremendously explain the difference between the two. And then one more thing I wanted us to touch on is earlier in the course we had some questions come up about coloring, and I know you guys don't require Pantone color system, but you have a color map that can help us match our colors at home. Can you talk to us a little about that? Sure, I have one. So we produce a color map that you can see here and it can be ordered through our website. And the reason this is useful is I'm sure as you know, and probably most of the people watching, colors as they appear on your computer screen and colors as they print, whether it's on your printer or something that you order, are not likely to match. And in fact if you walked around to a bunch of different computers and looked at your design on all of them it's likely that the colors wouldn't be exactly the same. So and then you add to that the limitations of the ink set that's being used, and reflective quality of the medium it's being printed on, and you realize that your monitor is actually a very limited tool of proofing color. So the way we've addressed that is by creating this map and what we have are small hex codes for each color on this piece of fabric, and if you have this fabric in front of you, and you're working with a digital file in Photoshop or Adobe Illustrator, you can put in this hex code, see the color on your screen, and use the color map as a physical reference for how that color on your screen is actually going to print on this particular fabric. Now on each of our fabrics it might be slightly different, but we do our best to maintain as much consistency between the different fabrics and other substrates as we can, although they're all a little bit different. But you can actually order this color map on any of the products that we sell. Yeah so you offer the color map on all of the different substrates. That's right. Okay. Does that make sense? Yes absolutely, and a substrate for you guys who don't know is exactly what he was talking about earlier. I think you offer 15, and it's cotton, it's I think you have a silk, and bunches of different kinds of fabrics that you can get printed on. That's right. Yeah, excellent. I think that all of my questions are answered, but if it's okay with you, we might open it up to the people who are watching? Sure. Alright great yeah we have some that are coming in from online, and we can start with this one, now this one is actually voted up, when you click that little blue arrow you can vote up the questions on our chat, and this one was voted up by five other people, so a lot of people are interested in this one. They want to know how well the Spoonflower printed cotton fabric for quilting lasts when it's washed and worn, versus traditionally printed cotton quilting fabric. Because they want to know if it'll, if the ink will soak in very well, so maybe you can speak a little bit about this for quilting. Right so one thing to, I have to digress a little bit to talk about the chemistry in that question. So there's really a couple of ways to put color on fabric, and broadly speaking you can either dye the fabric or you can print it using pigment. And a useful way to think about the difference between those two things is that dye gets inside the fiber whereas pigment sits on top, pigment is more like paint. As anyone whose dyed fabric knows, that's a process that requires some chemical preparation for the color, you have to add the color to the fabric and then you have to catalyze it somehow with steam or some kind of heat, and then a person's got to wash it to get all the extra dye out. So dye is an awesome way to create color on fabric, and in a perfect world that's the one you might always choose, but pigment is actually a much more economical and eco-friendly way of putting color on fabric, so pigments are literally just suspended particles of solid color. And when you put them on to fabric, you've got to use something, a polymer, to sort of link it. And that allows the pigment to hold on to the fiber when you rub it and when you wash it, so just for reference, blue jeans, traditionally colored with pigment, whereas a blouse or a scarf is traditionally going to be dyed. And pigment, again going back to blue jean example, does not hold up, the color does not hold up to repeated washing the same way that dyed fabric does. So it's, in that sense, inferior and wears, it gets an aged look over time. So there are lots of applications where that's okay, and somewhere it might not be desirable. All of our natural fiber fabrics, at least at this point, are colored using pigments. And that allows us to not have to operate with a lot of chemicals and not use as much water and other resources in the process. It also allows us to do it more quickly. And the color is more consistent from one week, and one month to the next. All of our synthetic fiber stuff is actually dyed, although it's dyed using a process called dye-supplemation, but the cool thing about these new fabrics like eco canvas and faux suede, is that the color, really is in that case, inside the fiber and you couldn't wash it out if you tried to. And it's also quite bright, so those colors you get much brighter colors with dyes than you do with pigments. Does that answer the question? Yeah I think that covers it, thank you. Alright now this other one comes from Rhiannon Pearson, she wants to know, should we use gradients on Spoonflower designs? You certainly can, so that's another important difference that I skipped over between screen printed designs and digitally printed designs, so a digital printing process can handle gradients and literally thousands of different colors within one image you don't have to do color separations. So you can literally print photos if you want to on fabric and it will look just as good as color separated files. So gradients are absolutely acceptable on digital, in the digital world. Okay great. Now do we have any questions here from our students, I know you guys have been eager. Okay go ahead Julie. I'm real excited to be talking to you, I've looked at your website before and only heard about it just recently, so just barely before I came and took the class. When you were mentioning the printing process on the different fabrics, do you recommend using any or some of the fabrics for garments, whether it's for you know making a toddler skirt or a woman's blouse. Cotton, knit, polyester, what kinds of things would you recommend if we were just making clothes for ourself or children or something, what's going to wear the best with washes and such? I wish you could come visit our office. Me too. On any given day, there are a dozen people walking around here wearing clothing entirely made from Spoonflower fabric they have made at home, so you would get lots of ideas from that. We have, in our house, I have three girls, and all of them have dresses and night gowns, and blankets all made from our fabric. We use, my wife has used our organic cotton knit for some of those things, which honestly the color doesn't hold up terrifically well, that's probably not the best fabric for color holding up, but it certainly holds up so you just get a nice weathered look, so if that's something that doesn't bother you then you can certainly use it. Now if you're looking for, and dry cleaning helps by the way if you're creating a dress and you want to dry clean it instead of washing it. Then the color is going to hold up better, but any of the new polyester fabrics, we have one called performance, sorry silky fail, which is great, which a lot of people around here are using for dresses. And those fabrics like I said, you can wash them as much as you want, you can use them for workout clothes if you wanted to make that from the polyesters. Great. Alright go ahead Kristen. Hi Stephen, I'm Kristen Ashley from Athens, Georgia so maybe I will come visit you one day. Awesome. My question is. I love Athens. Oh you did, awesome. My question is about the color map and you showed all the hex codes, do we have to use specifically those hex codes or does that just give us a reference? It's only there as a reference, you do not have to use the colors in the color map. Great, go ahead. And mine's kind of a simple question as well, my names Sharon hello. The uploading process, how simple is it, can you tell us what the biggest problems are, obstacles people have so we can avoid them? I will do my best, and I'm glad you asked that, thank you. So I know you all have been working with Adobe Illustrator in terms of the instructional material, but it's also possible to work with Photoshop or any other typical image editing, photo editing program and you can produce from that, a jpeg or a png, P - N - G file extension, and you want to save it if you can at 150 dots per inch. Which is the resolution that we sort of default to on our site. So one thing to check in your file, and rgb format by the way for color if you want to get in to that. One thing that you want to check for, you don't want a transparent background if you're using a png. You want to flatten it, flatten the file if you can before you upload it, and you want to check the edges of the file very carefully to make sure that there's not a stray line, that's one pixel wide and blank on one of the edges of the design. So that's something that's really easy to miss if you're looking at it on your screen, but if you upload that you probably won't see it in the preview, but when you get your fabric you'll definitely see the line if there's a blank pixel line in the file. Yeah and I'm going to show everyone after we are done with Stephen, I'm going to pull one of the patterns we made and show everyone how to save it for Spoonflower. We'll walk through that. Great now we have another question here, now this one, they want to know what is the best fabric to have the color map printed on to give the best idea of color across all fabrics? That's a good question. I think you know, if you want to get one on Kona cotton, or actually the cotton satin, the organic satin, which I think Bonnie was the one you said you liked. The satin has a nice smooth surface, so it holds lots of color, that's a good middle ground to go. The one significant difference that you're going to see is between the synthetic fiber and the natural fiber. If you were thinking about printing with a synthetic fiber it would be good to go ahead and get a color map there, because it's just going to be much brighter than the color map with the pigments. Anything from you Bonnie, any other questions that you want to touch on while we have Stephen here? You know, you have answered, I think all my questions, but I have been such a huge admirer of Spoonflower and what you guys are doing for the industry and the quilting, sewing industry. You're just opening up huge doors for us, and we really really appreciate it and I'm just so happy to have you here today. Thank you so much for saying that, and thank you for having me. Alright any final words from you Stephen, giving some advice to some of the designers out there who have been watching this course and ways that they can get involved with Spoonflower? You know the only piece of advice that I tell people, and I probably don't have to tell you all, because you're already artists and you're already engaged in this learning process, but don't be afraid to try new stuff. Some of the people that came to Spoonflower who are now, who have lines of fabric that are being distributed by fabric companies, are people who had never designed fabric before we came alone and we just, obviously they were terrific artists, but they just took the opportunity to try something new and to try out this new medium, so that is what the DIY world is all about. Trying new stuff and not being afraid to fail. That's my advice.
Class Materials
bonus material with purchase
Ratings and Reviews
Emily Leggett
I am so glad I took the time to sit through all 3 days of this course. I have been to hour long classes that I can't wait to get out of and this one I sat in for 3 days and I am wishing it wasn't over. I take a lot of continuing education classes and am always trying to learn new things and I have to say this is by far the absolute most informative, educational, inspiring, and motivating classes I have ever taken. Bonnie Christine was an amazing teacher. She took the time to take us through all aspects of the process and even beyond showing us so many things that can be done with everything she taught us in this class. I think she did a great job with the class, was easy to follow and is someone I would love to learn from again. Great job on everything. I would recommend this class to anyone who wants to learn about surface pattern design and Illustrator. Great job to everyone involved in putting this course together!
a Creativelive Student
Awesome awesome awesome course! Thank you Bonnie! Thank you Creative Live! I have learned so much... so much great information packed together in one class. I am so glad I bought the course so I can rewatch it any time I need to.
a Creativelive Student
I'm about halfway through my first viewing of the course and I have to say, its been electrifying! There is so much quality information here, its an excellent starting point, and I do think I can start working towards a career in design now. It also makes me want to find more information and courses in the art and design area. Bonnie is such a joyful, honest and enthusiastic instructor and really, it feels like she';s hosting an amazing party for her friends. Thank you Bonnie for doing this course and thank you CreativeLive for pricing it so affordably