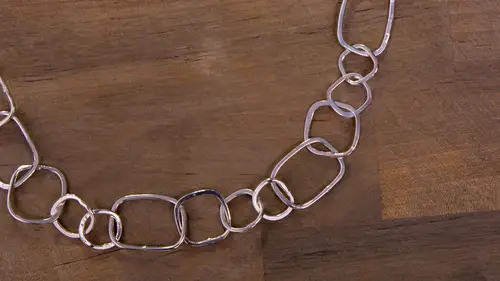
Lessons
Lesson Info
Creating Jump Rings
So chain making so the beauty of chain making is once you have this skill you don't have to necessarily by the mass produced chain you can add your own flair to it you can kind of make getting size you want you can um you know, if you're making embellish parts, you can men use unique chain to attach them to it's not necessarily something that has to be a generic it's making it more personal make it more your style, your aesthetic. So this is the piece here that we're going to be making, so I'm gonna talk about the basics of making jumper rings and I'm going to show you and we have most of these sizes, precut, but I'll talk about how you can no set up yourself to make your individual jump brings how to kind of create the shape here that you're seeing little flattened sole detail kind of a little flair to it, and then I'll talk to you about using a certain machine to give it that's nice, beautiful finish that you're seeing here as well as how to solve your links together a little more tr...
icky little different type of saada ring so walk you through those steps as well, but let's start so we're using fourteen gauge wire sterling silver wire to create um are shapes here now um, you can use round els um rectangular dell's what not this is just one way to actually create your jump ring so I'm just taking a wooden del so he could find a craft store I'm going to drill a hole in it so let me mount at any size job it is fine a thing that's a little bit bigger than the wire you are using because you want to place the wire in it some people use there's many different kind of d I y ways of creating your own little mounts for making these jump rings I know people who views like steel and they've bent a little kind of corner a shape into it you can use I've seen knitting meals used nice sturdy round object so we'll take our wooden dowel here though you know the drill a hole on one side is a square del all the way through now we have a spot for a wire to sit into now you can pre and neil this wire kind of help you shape it a little bit better, which I have done so I'm going to take some flat pliers here and I'm going to just be bend a line like that in it and that's what's going to slip into this hole but I just drilled all right now I'm going to do this by hand we never physically holding the down I'm gonna wrap this around it if, um you find that to be a bit cumbersome then you can place the dow into a vice and where the vice jaws air here gripping it he also keep the wire in place to and then you can use the tension of and wrap it around the dell I'm just since this is not very thick wire it's also not very it's often because I kneeled it I can just physically wrap it around using the tension here tio get the shape I want now when you're doing it this way if you're trying to go for a tight square shape a tight square jump bring as they refer to that's what these individual links for a chain are referred to in the jewelry world or his jump brings so you can if you want to tighten it up a little bit if you look at it on end you can kind of see that it might have gotten a little curve is not quite tight on the mandrell here our base or structure for create the shape so you can kind of just grab when your tools here take it over to just hammer ever so lightly all the way around now kind of create the shape that you are so once I've come to the end of my wire I'm just saw my jump rings so we are needing to kind of cut the edges first so they grab from flush cutters here and so it's attached here at the end into that hole where we started soto loosen it up so it'll slide off of our base here I am going to just kind of clip that wire off should fall through the other side kontic suppliers and pull that extra piece of metal out and now you can see that it can shift here on the mandrell we're going to bring it to the end of the mandrell here like that so we can saw now keeping in mind that we're creating jump rings that are we wanted to touch go end to end like this so we want this to be a nice flush clean connection this is what we're selling it by hand sort of using wire cutters, that's something that people you ask a lot about why can't use wire cutters to cut all these individual ones? Well, as you may have noticed, we're going close up on this this create a little kind of point little peek here when you use the wire cutters it's not a flush cut, and so if you use those, you're gonna have that and you're gonna have it won't be a seamless connection and what we're gonna eventually do assad our joints closed of every single jump a ring s so it's a really sturdy, really strong chain, every link is connected well and as you may remember in previous classes like you got a chance to check them out they they you need that strong connection for the but joint um and so we want to solve it by hand once again using a three out saw blade where we started cut we gotta think of where these end point so that's why I was bringing it up so we want to get the most from our cut here otherwise we're gonna have a lot of excess medal so I'm going to start kind of on the edge of where that cut is you have to decide which wire you want to focus on whether it's this end spot essentially the wire where you started or this one over here so going to bring it to the end here and I'm gonna start sawing down I was selling at an angle it may skip a little bit of first be mindful of your fingers bonnie when you're selling that are you putting the pressure on the saw itself or you keeping the soft here it is and then you're like moving the dowel toward you so I'm sorry say that question again shirt so when you're selling that are you actually when you're so are you putting the pressure on the saw to move forward or you moving the dowel towards yourself in keeping this are the saw blade relatively stable you're always cutting forward massage is always going forward and I can shift push the jump rings coil essentially forward a little bit as I go but you need tio always you're always coming on the down strokes you're always kind of bring it forward and you're going into the wood a little bit it's going to affect your tool essentially slips right off there but you you're not I mean you're super concerned about that you can worry about it otherwise don't worry about it too much once again if you're using a studio base like metal steel what have you it will in b I mean it won't mar up the structure too much when if you saw into it so now that we have our jump rings we're ready to shape them so I'm gonna be there for different reference points here so four different templates or temple sizes that we're going to be making job brings in some kind of see this here is a large size medium size which we just cut a small size and a kind of third in between size really close to your small size but well if you may notice on the bigger piece there are finished piece there is a great asian that we're doing size wise and so the first two links here the smaller ones are um not a big difference between them but when you see it all in line together it's actually really nice creation so once we have all four sizes cut and basically to create this eighteen inch sixteen inch chain it will be about seven to eight jump rings of each size ok and once again in the temple it's that you can download there actually tells you those various sizes and these dolls a lot of the sizes can be found a lot of craft stores so it's an accessible size if you'd like tio do the square pattern that we have here if you want to do it round then you I believe there's a rest one point in our templates to that as well so we have our shapes kind of put together here now we're going to flatten them now if you find that you can do two different things right now now we haven't really work hard in the metal very much so so I could go straight into hammering it which I'm going tio if you really want to make sure that you want to get a nice flattened look or you think you're going to flatten it a lot given a really broad texture and you kind of see here when you look at it close up that you know how wide that area can be totally depends on what were you like so if you had wanted to be more substantial than you would a needle all of your jump rings individually so but we're going to move on somebody come over here tio my hammering area and I'm going tio use my still block here and I'm actually going to use a plan ishan hammer that's what this particular tool is now plan ish ing hammers have a flat side and it curves up now to create this look and even impression it's better to use the flat side now when you're not used to using hammers like this, it can be a little tricky because it's, since it's flat, that means you have to hit directly straight on top of the piece of metal. If you angle it at all, it will, it can create, divots marks, but when you hit it straight on it's a nice, beautiful flat shape now the curve side the curve side is really great for doing for jane, which is something that we'll be covering in a another class that that also create these highs and lows it'll look really bub beyond the surface, it'll have to involve filing and standing to get that out. Eso it may take a little practice initially to try to get this straight on, but we're used the flat side because it will speed up your process, so I'm just going to choose to not to hammer on to where my joints is right now because that will kind of misshapen a little too much when I have to saw her it later, so he's gonna hammer be mindful of your fingers and once again, so you might notice that it's starting to stretch in certain areas returned to get a broader shape kind of see that they're a little dirty when you hammering um, depending on where you want us to expand, this becomes a kind of an aesthetic thing like, where do you want that to white? So if you want to be wider into one spot, you're gonna focus on that area is going to stretch out, and so it's kind of a matter of preference, you want to focus on the corner? Do you want to focus on this whole ben, so to bend or, you know, all the way around? So now we have our flattened jump, a ring and you're going to do that to every jump ring and to whatever degree that she would like to, stylistically speaking, then they may notice it got a little misshapen, so we're going to take our pliers to kind of give it back to that square shape, so I'm going to start with my flat players, and I'm just going to just hold it with my fingers and pushed that back into the square shape. This top edge has gotten a little wonky from being cut, so I'm just kind of grabbing in here and I'm pushing it in and I'm pushing that down there so they meet together again now we're basically going to be a saw during every ring together, jump bring together, and so you want that to be a nice, clean but joy. Remember, no gaps in our sauder seems so well, make sure that's nice in connected there. Sometimes what you can do and says, this is really thin wire, you can use your hands, you have to really use the players, you kind of push it past itself like that and pop it back, and then it helps. The tension helps it pop together, just like that. Now, once you have all that cut, you could have done quick adjustments. Such is that after you've hammered each one, you can start assembling in the few assembled here, so I'm gonna start with my bigger one. Actually, it's flattened this guy out a little bit, just to give a little dimension.
Class Materials
bonus material with purchase
Ratings and Reviews
Judy Craik
I thought Bonnie was very informative, however I didn’t like the camera angles. Most classes I take, the focus is the table and shows the teachers hands. Thank you Bonnie, I enjoyed you short class.